Отличие таврового шва от углового. Сварные швы и соединения
В процессе выполнения сварочных работ получаются различные соединения. Сварочные швы способны соединять не только металлы, но и другие разнородные материалы. Состыкованные в неразъемный узел элементы представляют собой соединение, которое можно разграничить на несколько участков.
Зоны сварочного соединения
Соединение, полученное в процессе сварки, разбивают на такие зоны:
- Место сплавления - граница между основным металлом и металлом полученного шва. В этой зоне находятся зерна, которые отличаются по своей структуре от состояния основного металла. Происходит это из-за частичного расплавления во время сварочного процесса.
- Область термического влияния - зона основного металла, которая не подверглась оплавлению, хотя в процессе нагрева металла структура ее была изменена.
- Сварочный шов - участок, который образовался во время кристаллизации в процессе остывания металла.
Типы сварочных соединений
В зависимости от расположения стыкуемых изделий друг относительно друга соединения делятся на такие типы:
- Встык. Состыковка элементов конструкции осуществляется в одной плоскости торцами друг к другу. В зависимости от различной толщины соединяемых деталей торцы могут относительно друг друга вертикально смещаться.
- Угловое соединение. В этом случае совмещение торцов производится под углом. Сварочный процесс осуществляется на примыкающих краях деталей.
- Соединение внахлест. Детали под сварку расположены параллельно с частичным перекрытием.
- Торцевое соединение. Свариваемые элементы совмещены параллельно друг другу и состыкованы по торцам.
- Тавровое соединение. В этом случае торец одной детали примыкает к боковой части другой под углом.
Сварочные соединения также характеризуют виды сварочных швов, квалифицировать которые можно по некоторым признакам.
Показатели сварного шва
Существует несколько параметров, по которым можно охарактеризовать все полученные сварочные швы:
- ширина - это размер между границами шва, которые прорисовываются видимыми линиями сплавления;
- корень шва - обратная его сторона, которая находится в максимальной удаленности от лицевой части;
- выпуклость - определяется в наиболее выпуклой части шва и обозначается расстоянием от плоскости основного металла до границы наибольшего выступа;
- вогнутость - этот показатель актуален, если имеет место в сварном шве, потому что, по сути, является дефектом; определяется данный параметр в том месте, где шов имеет наибольший прогиб - от него до плоскости основного металла измеряется размер вогнутости;
- катет шва - он имеет место только в угловом и тавровом соединении; измеряется этот показатель наименьшим расстоянием от боковой поверхности одной свариваемой детали до ограничительной линии шва на поверхности второй.
Виды швов по способу выполнения
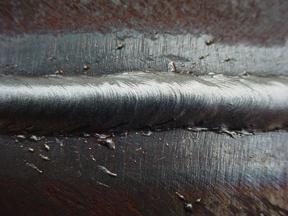
Виды сварочных швов по пространственному положению и протяженности
Различают такие положения сварки:
- нижнее, когда свариваемый шов находится в нижней горизонтальной плоскости, т. е. под углом 0º относительно земли;
- горизонтальное, направление сварки ведется горизонтально, а деталь может находиться под углом от 0º до 60º;
- вертикальное, в этом положении свариваемая поверхность находится в плоскости от 60º до 120º, и сварка ведется в вертикальном направлении;
- потолочное, когда работа проводится под углом 120-180º, то есть сварочные швы расположены над мастером;
- "в лодочку", это положение относится только к угловым или тавровым соединениям, деталь выставляется под наклоном, и сварка ведется «в угол».
Разбивка по протяженности:
- непрерывные, так выполняются практически все швы, но бывают и исключения;
- прерывистые швы, они имеют место только в угловых соединениях; двухсторонние швы такого типа могут выполняться как в шахматном, так и в цепном порядке.
Разделка кромок
Эта конструктивная особенность применяется в том случае, когда толщина металла, используемого для сварки, больше размера 7 мм. Разделка кромок - это удаление металла с кромок в определенной форме. Данный процесс выполняется при однопроходной сварке стыковых швов. Это необходимо для того, чтобы получить правильный сварочный шов. Что касается толстого материала, разделка необходима для того, чтобы проплавить первоначально корневой проход и затем следующими наплавляемыми валиками, равномерно заполняя полость, проварить металл по всей толщине.
Разделку кромок можно выполнять, если толщина металла не меньше 3 мм. Потому что более низкое ее значение приведет к прожогам. Разделка характеризуется такими конструктивными параметрами: зазор - R; угол разделки кромок - α; притупление - с. Расположение этих параметров показывает чертеж сварочного шва.
Разделка кромок увеличивает количество расходных материалов. Поэтому данную величину всячески пытаются минимизировать. Она подразделяется на несколько видов по конструктивному исполнению:
- V-образная;
- X-образная;
- Y-образная;
- U-образная;
- щелевая.
Особенности разделки кромок
Для малых толщин свариваемого материала от 3 до 25 мм обычно применяется односторонняя V-образная разделка. Скос может выполняться на обоих торцах или на одном из них. Металл толщиной 12-60 мм целесообразно сваривать с двухсторонней X-образной разделкой. Угол α при разделке в X, V форме равен 60º, если скос выполняется только на одной кромке, тогда значение α будет равно 50º. Для толщины 20-60 мм наиболее экономным будет расход наплавляемого металла при U-образной разделке. Скос также может быть выполнен по одному или по обоим торцам. Притупление составит 1-2 мм, а значение зазора будет равно 2 мм. Для большой толщины металла (свыше 60 мм) самым эффективным способом будет щелевая разделка кромок. Для сварного соединения очень важна данная процедура, она влияет на несколько факторов шва:

Стандарты и ГОСТы
- Ручная Сварочные швы и соединения по ГОСТу 5264-80 включают типы, конструктивные размеры для сварки, покрытые электродами во всех пространственных положениях. Сюда не входят только трубопроводы из стали.
- Сварка стальных трубопроводов. ГОСТ 16037-80 - определяет основные типы, разделку кромок, конструктивные размеры при механизированном способе сваривания.
- Сварка трубопроводов из меди и медно-никелевых сплавов. ГОСТ 16038-80.
- Дуговая сварка алюминия. ГОСТ 14806-80 - форма, размеры, подготовка кромок для ручной и механизированной сварки алюминия и его сплавов, процесс выполняется в защитной среде.
- Под флюсом. ГОСТ 8713-79 - сварочные швы и соединения выполняются автоматической или механизированной сваркой на весу, на флюсовой подушке. Распространяется на толщину металла от 1,5 до 160 мм.
- в ГОСТ 27580-88 - стандарт на ручную, полуавтоматическую и Она выполняется неплавящимся электродом в инертных газах с присадочным материалом и распространяется на толщину алюминия от 0,8 до 60 мм.
Обозначение сварочного шва
Согласно нормативным документам наличие сварочных швов показывается на или на общем виде. Изображаются сварочные швы сплошными линиями, если они видимые. А если наоборот - то штриховыми отрезками. От данных линий отводятся выноски с односторонними стрелками. Условное обозначение сварочных швов выполняется на полке от выноски. Надпись делается над полкой, если шов находится на лицевой стороне. В обратном варианте обозначение будет находиться под полкой. Сюда включается информация о шве в такой последовательности:
- Вспомогательные знаки. На пересечении выноски с полкой может стоять значок:
○ - замкнутый шов;
┐ - сварка шва производится при монтаже.
- Обозначение сварочных швов, их конструктивных элементов и ГОСТ соединения.
- Наименование шва по стандарту.
- Способ сварки по нормативным стандартам.
- Указывается катет, этот пункт касается только угловых соединений.
- Прерывистость шва, если таковая имеет место. Здесь указывается шаг и расположение отрезков сварки.
- Дополнительные значки вспомогательного значения. Рассмотрим их отдельным пунктом.
Вспомогательные обозначения
Эти знаки также наносятся сверху полки, если сварочный шов на чертеже видимый, и под ней, когда невидимый:
- ---снятие усиления шва;
- обработка поверхности, которая обеспечит плавный переход к основному металлу, исключив наплывы и неровности;
- шов выполняется по незамкнутой линии; этот знак применяется только к видимым на чертеже сварочным швам;
- чистота обработки поверхности сварного соединения.
Для упрощения, если все швы конструкции выполнены по одному ГОСТу, имеют одинаковые разделки кромок и конструктивные размеры, обозначение и стандарт на сварку указываются в технических требованиях. В конструкции могут быть не все, но большое количество одинаковых швов. Тогда их разбивают по группам и присваивают им порядковые номера в каждой группе в отдельности. На одном шве указывают полное обозначение. На остальных ставят только порядковые номера. Количество групп и число швов в каждой из них должно быть указано в нормативной документации.
Сварным соединением называется неразъемное соединение, выполненное сваркой, состоящее из двух деталей и соединяющего их сварного шва.
ГОСТ 5264-80 устанавливает основные типы, конструктивные элементы и размеры сварных соединений из сталей, а также сплавов на железоникелевой и никелевой основах, выполняемых ручной дуговой сваркой металлическим электродом при толщине свариваемого металла до 175 мм. Установлены слудующие типы соединений: стыковые - условное
обозначение С, нахлесточные - Н, тавровые - Ти угловые - У.
Стыковые соединения - самые типичные сварные соединения, в которых торцы или кромки соединяемых деталей располагаются так, что поверхность одной детали является продолжением поверхности другой детали. Стыковые соединения без скоса свариваемых кромок применяют при соединении листов толщиной до 12 мм. Кромки листов срезают под прямым углом к плоскости листа и при сварке располагают с зазором 1 ... 2 мм. Листы толщиной до 4 мм сваривают односторонним швом, 2... 12 мм - двусторонним швом. Стыковые соединения с V-образной разделкой кромок применяют при сварке металла толщиной 3 ... 60 мм. При этом разделка кромок может быть одно - и двусторонней. Для толщин металла 15 ... 100 мм применяют V-обр. азную разделку шва с криволинейным скосом одной или обеих кромок. Стыковые соединения с X - и К - образной разделкой кромок применяют при сварке металла толщиной 8... 175 мм. При этом расход электродного металла, а отсюда и электроэнергии почти вдвое меньше, чем при V-образной разделке кромок. Кроме того, такая разделка обеспечивает меньшую величину деформаций после сварки. При V - и Х-образной разделках кромки притупляют, чтобы предотвратить прожог металла при сварке.
Нахлесточные соединения широко применяют при изготовлении различных строительных конструкций - колонн, мачт, ферм и др. Один элемент соединения накладывается на другой. Величина перекрытия должна быть не менее удвоенной суммы толщин свариваемых кромок изделия. Свариваемые поверхности не обрабатывают (не считая зачистку кромок). Листы при сварке заваривают с обеих сторон, чтобы не допустить проникновения влаги в зазор между свариваемыми листами.
Тавровые соединения - соединения, при которых торец одного элемента примыкает к поверхности другого элемента свариваемой конструкции под некоторым углом (чаще всего под прямым). В зависимости от назначения соединения и толщины металла элементов конструкции сварка может быть осуществлена без скоса, с одно - и двусторонним скосом кромок элементов соединения. Для получения прочного шва зазор между свариваемыми элементами составляет 2 ... 3 мм.
Угловые соединения осуществляют при расположении свариваемых элементов под прямым или произвольным углом и сварка выполняется по кромкам этих элементов с одной или с обеих сторон. Угловые соединения применяют при сварке различных коробчатых изделий, резервуаров и емкостей.
Сварные швы подразделяют по следующим признакам: по положению относительно действующей силы (рис. 39) - на фланговые (а), лобовые (б) и косые (в); по положению в пространстве (рис. 40) - на нижние (а), горизонтальные (б), вертикальные (в) и потолочные (г); по внешней форме (рис. 41) - на выпуклые (а), нормальные (о) и вогнутые (в); по протяженности (рис. 42) - на непрерывные или сплошные (а) и прерывистые (б).
Выпуклые швы имеют большее сечение и поэтому называются усиленными. Однако большая выпуклость для швов, работающих при знакопеременных нагрузках, вредна, так как вызывает концентрацию напряжений в местах перехода от шва к поверхности основной детали. Вогнутые швы, ослабленные, применяют, как правило, в угловых соединениях; в стыковых соединениях они не допускаются. Нормальные швы по сечению соответствуют расчетным и приняты как основной вид сварного шва. Прерывистые швы применяют в том случае, если шов неответственный (сварка ограждений, настила и др.) или если по прочностному расчету не требуется сплошной шов. Их применяют в целях экономии материалов, электроэнергии и труда сварщика. Длину I провариваемых участков прерывистого шва принимают 50... 150 мм, а промежутки девают примерно вдвое больше. Расстояние от начала предыдущего шва до начала последующего шва называют шагом шва t.
Основные типы сварных швов: стыковые и угловые. Стыковые швы - это швы стыковых соединений. Угло-
|
Вые швы, называемые также Валиковыми, - это швы угловых, тавровых и нахлесточных соединений. ГОСТ 2.312-72 ЕСКД устанавливает условные изображения и обозначения сварных соединений в конструкторских документах изделий. Условное обозначение шва наносят на полке линии-выноски, проведенной от изображения шва с лицевой стороны, и под полкой линии-выноски, проведенной от изображения шва с оборотной стороны. На рис. 43 показан пример обозначения шва стыкового соединения с криволинейным скосом одной кромки, двустороннего, выполняемого ручной дуговой сваркой при монтаже изделия. Уснленне снято с обеих сторон. Шероховатость поверхности шва с лицевой стороны - Rz20, а с оборотной стороны - #г40.
§ 15. Выбор режима сварки
и техника выполнения швов
Для выполнения сварного шва прежде всего определяют режим сварки, обеспечивающий хорошее качество сварного соединения, установленные размеры и форму при минимальных затратах материалов, электроэнергии н труда.
Режимом сварки называется совокупность параметров, определяющих процесс сварки: вид тока, диаметр электрода, напряжение н сварочный ток, скорость перемещения электрода вдоль шва и др. Основными параметрами режима ручной дуговой сварки являются диаметр электрода и зна-
Толщина свариваемых кромок, мм <2 3...5
Диаметр электрода, мм <2 3...4
При выполнении угловых и тавровых соединений принимают во внимание значение катета шва: при катете
3 ... 5 мм сваривают электродами диаметром 3... 4 мм, а при катете 6 ... 8 мм - электродами диаметром
4 ... 5 мм. При многопроходной сварке швов стыковых соединений первый проход выполняют электродом диаметром не более 4 мм; это необходимо для хорошего провара корня шва в глубине разделки.
1 ГОСТ 5264-80-013 д№<> |
чение сварочного тока. Остальные параметры выбирают в завнснмостн от марки электрода, положения свариваемого шва в пространстве, вида оборудования и др.
Диаметр электрода устанавливают в зависимости от толщины свариваемых кромок, вида сварного соединения и размеров шва. Для стыковых соединений приняты практические рекомендации по выбору диаметра электрода в зависимости от толщины свариваемых кромок.
6.. .8 9...12 13...15 16...20 >20
4.. .5 5...6 6...7 7...8 8...10
По выбранному диаметру электрода устанавливают значение сварочного тока. Обычно для каждой марки электродов значение тока указано на заводской этикетке, но можно также определить его по формулам:
/ = (40...50) d3 при йэ = 4...6 мм; / = (20 + 6 йз) d3 при йз<4 мм и йэ> 6 мм,
где / - сварочный ток, А; йэ - диаметр электрода, мм.
|
Полученное значение сварочного тока корректируют, учитывая толщину металла и положение свариваемого шва. При толщине кромок (1,3 ... 1,6) d, расчетное значение сварочного тока уменьшают на 10...15%, а при толщине кромок > 3d, - увеличивают на 10... 15%. Сварку вертикальных и потолочных швов выполняют сварочным током, на 10... 15% уменьшенным против расчетного.
Сварочную дугу возбуждают двумя приемами. Можно коснуться свариваемого изделия торцом электрода и затем отвести электрод от поверхности изделия на 3... 4 мм, поддерживая горение образовавшейся дуги. Можно также быстрым боковым движением коснуться свариваемого изделия и затем отвести электрод от поверхности изделия на такое же расстояние (по методу зажигания спички). Прикосновение электрода к изделию должно быть кратковременным, так как иначе он приваривается к изделию («примерзает»). Отрывать «примерзший» электрод следует резким поворачиванием его вправо и влево.
Длина дуги значительно влияет на качество сварки. Короткая дуга горит устойчиво и спокойно. Она обеспечивает получение высококачественного шва, так как расплавленный металл электрода быстро проходит дуговой промежуток и меньше подвергается окислению и азотированию. Но слишком короткая дуга вызывает «примерзание» электрода, дуга прерывается, нарушается процесс сварки. Длинная дуга горит неустойчиво с характерным шипением. Глубина проплавления недостаточная, расплавленный металл электрода разбрызгивается и больше окисляется и азотируется. Шов получается бесформенным, а металл шва содержит большое количество оксидов. Для электродов с толстым покрытием длину дуги указывают на заводской этикетке.
В процессе сварки электроду сообщаются следующие движения (рис. 44): а-по направлению оси электрода 1 в зону дуги. Скорость движения должна соответствовать скорости плавления электрода, чтобы сохранить постоянство длины дуги; б - вдоль линии свариваемого шва 2. Скорость перемещения не должна быть большой, так как металл электрода не успеет сплавиться с основным металлом (непровар).При малой скорости перемещения возможны перегрев и пережог металла. Шов получается широкий, толстый. Производительность сварки оказывается низкой; в - поперечные колебательные движения применяют для получения уширенного валика шириной, равной 3 ... 4 йэ. Поперечные движения замедляют остывание направляемого металла, облегчают выход газов и шлаков и способствуют наилучшему сплавлению основного и электродного металлов и получению высококачественного шва. Образующийся в конце наплавки валика кратер необходимо тщательно заварить.
Техника выполнения сварных швов зависит от вида и пространственного положения шва.
Нижние швы наиболее удобны для выполнения, так как расплавленный металл электрода под действием силы тяжести стекает в кратер и не вытекает из сварочной ванны, а газы и шлак выходят на поверхность металла. Поэтому по возможности следует вести сварку в нижнем положении. Стыковые швы без скоса кромок выполняют наплавкой вдоль шва валика с небольшим уширением. Необходимо хорошее проплавление свариваемых кромок. Шов делают с усилением (выпуклость шва до 2 мм). После проварки шва с одной стороны изделие переворачивают и, тщательно очистив от подтеков и шлака, заваривают шов с другой стороны.
|
Сварку стыковых швов с V-образной разделкой при толщине кромок до 8 мм производят в один слой, а при большой толщине - в два слоя и более. Первый слой наплавляют высотой 3 ... 5 мм электродом диаметром 3 ... 4 мм. Последующие слои выполняют электродом диаметром 4...5 мм. Перед наплавкой очередного слоя необходимо тщательно очистить металлической щеткой разделку шва от шлака и брызг металла. После заполнения всей разделки шва изделие переворачивают и выбирают небольшую канавку в корне шва, которую затем аккуратно заваривают. При невозможности подварить шов с обратной стороны следует особенно аккуратно проварить первый шов. Стыковые швы с Х-образной разделкой выполняют аналогично многослойным швам с обеих сторон разделки. Угловые швы в нижнем положении лучше выполнять в положении «лодочка» (рис. 45, а). Если изделие не может быть так установлено, необходимо особенно тщательно обеспечить хороший провар корня шва и свариваемых кромок. Сварку следует начинать с поверхности нижней кромки и затем переходить через разделку шва на вертикальную кромку, как показано на рис. 45, б. При наложении многослойного шва первый валик выполняют ниточным швом электродом диаметром 3 ... 4 мм. При этом необходимо обеспечить хороший провар
корня шва. Затем после зачистки разделки наплавляют последующие слои.
Вертикальные швы менее удобно сваривать, так как сила тяжести увлекает капли электродного металла вниз. Вертикальные швы следует выполнять короткой дугой и снизу вверх (рис. 45, в). При этом капли металла легче переходят в шов, а образующаяся полочка удерживает очередные капли металла от стекания вниз. Сварку можно вести и сверху вниз. При этом дугу следует зажигать при положении электрода, перпендикулярном плоскости изделия (положение /, рис. 45, г). После образования первых капель металла электрод наклоняют вниз 11 и сварку выполняют возможно короткой дугой. Рекомендуется применять электроды диаметром 4 ... 5 мм при несколько пониженном сварочном токе (150... 170 А).
Горизонтальные швы - для их выполнения подготавливают кромки с односторонним скосом у верхнего листа (рис. 45, д). Дугу возбуждают на нижней кромке и затем переводят на поверхность скоса и обратно. Сварку выполняют электродом диаметром 4 ... 5 мм. Горизонтальные нахлесточные швы (рис. 45, е) выполняются легче, так как нижняя кромка образует полочку, удерживающую капли расплавленного металла.
Потолочные швы наиболее трудно выполнимы и поэтому требуют высо-
кой квалификации сварщика. Применяют электроды диаметром не более 5 мм при уменьшенном сварочном токе. Следует применять тугоплавкое покрытие электрода, образующее «чехольчик», в котором удерживается расплавленный металл электрода. Дуга должна быть как можно короче для облегчения перехода капель металла электрода в кратер шва.
Выбор способа и порядка выполнения сварных швов зависит главным образом от толщины металла и протяженности шва. При сварке тонколистовой стали необходимо строгое соблюдение техники выполнения сварных швов. Особую опасность представляют сквозные прожоги и проплавление металла.
Сталь толщиной 0,5 ... 1,0 мм следует сваривать внахлестку с проплавлением через верхний лист (рис. 46, а) или встык с укладкой между свариваемыми кромками стальной полосы (рис. 46, б). Во втором случае расплавление кромок должно происходить при косвенном воздействии дуги. Сварку производят на пониженных режимах. Питание дуги - от преобразователя ПС-100-1 или аппарата переменного тока ТС-120, так как они отличаются повышенным напряжением холостого хода и малыми сварочными токами. Рекомендуются следующие режимы сварки:
TOC o "1-5" h z Толщина металла, мм Диаметр электрода, мм Сварочный ток, А. .
0,5 1,0 1,5 2,0 2,5
1 1,6...2 2 2,5 3
10.. .20 25...35 40...50 50...70 60.. .90
Применяют электроды с покрытием марок МТ или ОМА-2. Сварку ведут на массивных теплоотводящих медных подкладках. Такой способ теплоотвода предохраняет металл от сквозного прожога и способствует хорошему формированию шва. Тонколистовую сталь можно сваривать с отбортовкой кромок (рис. 46, в).
Сварку производят постоянным током неплавящимся электродом (угольным или графитовым) диаметром
6.. . 10 мм при сварочном токе 120... 160 А. Применение иных способов сварки тонколистового материала рассмотрено в соответствующих главах.
Металл большой толщины сваривают в несколько проходов, заполняя разделку кромок слоями. При толщине металла 15 ... 20 мм сварку выполняют секциями способом двойного слоя (рис. 47, а). Шов разбивают на участки длиной 250... 300 мм и каждый участок заваривают двойным слоем. Второй слой накладывают после удаления шлака по неостывшему первому. При толщине металла 20 ... 25 мм и более применяют сварку каскадом (рис. 47, б) или сварку горкой (рис. 47, в). Каскадный способ заключается в следующем. Весь шов разбивают на участки и сварку ведут непрерывно. Закончив сварку слоя на первом участке, сваривают первый слой на втором участке и продолжают сварку на первом участке, накладывая второй слой по неостывшему первому слою, и т. д. Сварка горкой является разновидностью сварки каскадом, обычно выполняется двумя сварщиками одновременно и ведется от середины шва к краям. Такие способы сварки обеспечивают более равномерное распределение температуры и значительное снижение сварочных деформаций.
Способы выполнения сварных швов по длине зависят от их протя
женности. Условно принято различать: короткие швы длиной до 250 мм, средние швы длиной 250... 1000 мм и длинные швы протяженностью более 1000 мм. Короткие швы выполняют сваркой на проход (рис. 48, а). Швы средней длины сваривают либо от середины к краям (рис. 48, б), либо обратноступенчатым способом (рис. 48, в). Обратноступенчатый способ заключается в том, что весь шов разбивают на участки и каждый участок сваривают в направлении, обратном общему направлению сварки. Конец каждого участка совпадает с началом предыдущего. Длина участка выбирается в пределах 100... 300 мм в зависимости от толщины металла и жесткости свариваемой конструкции. Длинные швы сваривают также обратноступенчатым способом.
|
Сварка при низких температурах отличается следующими основными особенностями. Стали изменяют свои механические свойства, понижается ударная вязкость и уменьшается угол загиба, ухудшаются пластические свойства и несколько повышается хрупкость, а отсюда склонность к образованию трещин. Это особенно заметно у сталей, содержащих углерод более 0,3%, а также у легированных сталей, склонных к закалке. Металл ванны охлаждается значительно быстрее, а это приводит к повышенному содержанию газов и шлаковых включений и, как следствие, - к снижению механических свойств металла шва. В связи с этим установлены следующие ограничения сварочных работ при низкой температуре. Сварка стали толщиной более 40 мм при температуре 0°С допускается только с подогревом. Подогрев необходим для сталей толщиной 30 ... 40j мм при температуре ниже
|
10°С, для сталей толщиной 16... 30 мм при температуре ниже - 20°С и для сталей толщиной менее 16 мм при температуре ниже - 30°С.
Для подогрева применяют горелки, индукционные печи и другие нагревательные устройства. Сварку производят электродами типа Э42А, Э46А, Э50А, обеспечивающими высокую пластичность и вязкость металла шва. Сварочный ток на 15...20% выше нормального. Рабочее место должно быть защищено от ветра и снега.
§ 16. Высокопроизводительные способы сварки
Сварка с глубоким проплавлением
(методом опирання). Для получения глубокого проплавления используют электрод 4 (рис. 49) с утолщенным покрытием. Стержень электрода плавится быстрее покрытия, поэтому на конце электрода образуется «чехольчик». Опираясь этим чехольчиком на кромки свариваемого изделия, перемещают электрод вдоль шва 3 без колебательных движений (1 - шлак, 2 - металл шва, 5 - основной металл). Для получения узких швов
|
|
|
Такой метод обеспечивает повышение производительности сварки на 50 ... 70% за счет уменьшения расхода наплавляемого металла на единицу длины шва. Короткая дуга и большая концентрация теплоты значительно увеличивают глубину проплавления основного металла. В закрытой чехольчиком зоне дуги потери металла на угар и разбрызгивание минимальные. Сварочный ток может быть повышен на 40 ... 60% по сравнению с нормальным. Метод особенно эффективен при сварке угловых и тавровых соединений в нижнем положении или «в лодочку». Основным электродом для сварки с глубоким проплавлением является ЦМ-7с. Менее эффективно применение электродов ОММ-5, МЭЗ-04. Сварка таким методом не требует высокой квалификации и легко осваивается сварщиком.
Сварка пучком электродов (рис. 50). Два или несколько электродов с качественным покрытием связывают в двух-трех местах по длине тонкой проволокой, а оголенные от покрытия концы прихватывают сваркой. Через электрододержатель ток подводится одновременно ко всем электродам. Дуга возбуждается на том электроде, который ближе к свариваемому изделию. По мере проплавления дуга переходит от одного электрода к другому. При таком методе электрод нагревается значительно меньше, что позволяет работать при больших токах. Например, при трех электродах диаметром 3 мм допустимый сварочный ток достигает 300 А. Потери металла на угар и разбрызгивание не возрастают. При этом, производительность сварки повышается в 1,5 ... 2 раза. Коэффициент наплавки электродов увеличивается, так как стержни электродов все время подогреваются теплотой дуги. Однако пучком электродов невозможно обеспечить хороший провар корня шва. Поэтому приходится предварительно одиночным электродом проваривать корень разделки и затем производить сварку шва пучком электродов. Этот метод дает высокую производительность при наплавочных работах.
Сварка трехфазной дугой. Сварка осуществляется двумя электродами, изолированными друг от друга (рис. 51, а). К электрододержателю подводят две фазы источника тока, а третью фазу подводят к свариваемому изделию. Возбуждаются и одно
временно горят три сварочные дуги: по одной между каждым электродом и изделием и третья между электродами. Такая схема значительно повышает устойчивость горения дуги, улучшает степень использования теплоты дуги и позволяет снизить напряжение холостого хода. Для сварки применяют электроды марок ЦМ-7, ОММ-5. УОНИ-13.
При сварке трехфазной дугой применяют также следующие схемы: сварку двумя одинарными электродо - держателями (рис. 51, б); сварку одним одинарным электрододержателем и вторым электродом, уложенным в разделку шва изолированно от свариваемого изделия (рис. 51, в); сварку пучком электродов, из которых только два токоведущие, а остальные холостые (т. е. не включены в сварочную цепь и расплавляются от теплоты дуги). Сварка трехфразной дугой применима при любых соединениях в нижнем и наклонном положениях. Такой метод особенно можно рекомендовать для сварки в нижнем положении и «в лодочку» угловых и тавровых соединений.
Сварка ванным способом. Ванный способ применяют при сварке стыков арматуры железобетонных конструкций (рис. 52, а). Сущность
способа заключается в следующем: к стержням арматуры в месте стыка приваривают стальную форму, в которой теплотой дуги создают ванну расплавленного металла, непрерывно подогреваемую дугой. От теплоты металла ванны плавятся торцы свариваемых стержней, образуется общая ванна металла шва и затем при остывании - сварное соединение. При сварке вертикальных швов в качестве формующей детали применяют штампованную форму из листовой стали (рис. 52, б), которую приваривают к нижнему стержню. Затем прихватывают конец верхнего стержня к нижнему и переходят к заполнению формы наплавляемым металлом. Для выпуска шлака прожигают электродом отверстия в стенке формы, которые затем заваривают. Процесс сварки ведут при больших токах. Например, для электродов диаметром 5...6 мм сварочный ток достигает 400... 450 А. Сварку при низких температурах выполняют током выше установленного на 10... 12%. Зазор между торцами свариваемых стержней должен быть не менее удвоенного диаметра электрода. Сварку можно выполнять одним или несколькими электродами одновременно. Рекомендуется применять электроды марки УОНИ-13/55 (типа Э50А). Ванный способ значительно уменьшает расход электродов и электроэнергии и снижает трудоемкость и себестоимость сварочных работ.
- Разновидность сварных точек по типу соединения
- Различные виды сварочных швов
- Геометрия сварочных швов
- Нормы использования сварки на величину шва
Участок металлической структуры, в которой объединяются разные детали при эксплуатации сварки, называется сварочным соединением. Сварные швы могут быть различными по прочности. Сварочное соединение может включать в себя один сварной шов. Это место термического воздействия на точку соединения металлов. В результате такого воздействия металл расплавляется, а при остывании кристаллизуется. Во многом на качество шва влияет характеристика металла в точке термического воздействия.
Разновидность сварных точек по типу соединения
Швы стыковые используются в стыковых соединениях. Выполняются они неотрывными. Отличием являются действия по подготовке плоскости в торце сечения и элементов, подготавливаемых к контакту. Благодаря этому открывается полный доступ к месту сварки и обеспечивается максимально эффективное проваривание плоскостей на всю толщину.
Среди стыковых швов можно различить разные виды:
- Односторонние и двухсторонние без распилки краев.
- С односторонней или двухсторонней распилкой одного из краев.
- С односторонней распилкой обоих краев.
- Распилкой V или X-вида.
- Двухсторонней распилкой обоих краев.
Угловой тип соединений применяют, когда нужна сварка угловых швов. В изготовлении таких соединений используются угловые швы. Разделить их можно по беспрерывности и по зазору.
Дополнить вышеуказанные виды можно еще разновидностью, относящейся и к стыковым, и к угловым. Таковыми служат пробочные и прорезные разновидности. Прорезной тип используется, когда нужно верхний пласт, а возможно, и нижележащие, проплавить до основного элемента. В контакте утолщенных пластов прорезные швы и соединения выполняются по изготовленным жерлам. В таком виде они будут называться “пробочными” или в случае дуговой сварки «электрозаклепкой».
Вернуться к оглавлению
Различные виды сварочных швов
Различия сварки и виды сварочных швов по пребыванию в пространстве:
- сварка горизонтальных швов;
- сварка потолочных швов;
- нижние швы.
Применяется при сварочных работах, находящихся снизу на ровной плоскости. Они технически простейшие по исполнению. Высокая прочность стыков объясняется удобными условиями, в которых растопленный металл под своим весом устремляется в сварную ванну, которая расположена горизонтально. Эта работа самая легкая в исполнении и за ней легко уследить. В нахлесточных структурах угольные в нижней позиции выполняются непрерывными, без производства поперечных колебаний.
Горизонтальные сварные швы. Ход сваривания горизонтальных точек связан с некоторыми трудностями. В ходе сваривания поперечным швом на вертикальной поверхности расплавленный металл может стекать на нижний край. Как следствие на верхнем краю может появиться подрез. Использование этого способа в сваривании угольных точек, производимых в горизонтальном расположении, довольно простое и не вызывает каких-либо затруднений. Сама работа похожа на сварочные работы в нижнем расположении и зависит от требуемого шва.
Вертикальные сварочные швы. В сварке вертикально стоящих деталей расположенный снизу металл призван удерживать плавящийся металл сверху, но при этом он получается грубым и в виде чешуи. Значительно сложнее получить качественное соединение при работе, направленной вниз. Сварка вертикальных швов в стоячей плоскости возможна лишь в ориентации снизу вверх и наоборот.
Потолочные швы. Сложнейший по исполнению вид сварных работ. В процессе работы затруднено выделение газов и шлаков, а также сложно расплав удерживать от стекания и добиваться прочности точки. Но несмотря на соблюдение всех техник потолочной сварки, швы все равно уступают по надежности сварочным швам, исполненным в остальных позициях.
Классификация особенностей сварных соединений по очертанию:
- сварка продольных швов;
- создание кольцевых швов.
Для выполнения продольного типа сварочных работ требуется провести доскональную подготовку металла в точке предполагаемой сварки. Поверхности деталей должны быть очищены от заусениц, кромок и неровностей. В работе продольной сварки шов возможен только при полной очистке и обезжиривании требуемых поверхностей.
Кольцевые сварные швы. Сварные работы по окружностям требуют большой аккуратности и точности, тут же необходима калибровка сварочных токов, особенно при работе с малыми диаметрами.
Сварка кольцевых швов различается по очертанию. Они бывают:
- выпуклые;
- вогнутые;
- плоские.
Вернуться к оглавлению
Геометрия сварочных швов
Основными геометрическими параметрами являются: ширина, изогнутость, выпуклость и корень стыка.
Шириной называется зазор между обозримо различными гранями сплавления металлов. Изогнутость – это зазор промеж площади, протекающей по обозримым граням точки сварки и определенного металла в точке предельной вогнутости.
Для измерения выпуклости определяется зазор относительно уровней, протекающий по обозримым граням шва и основного металла в точке предельной выпуклости. Корень – это предельно отдаленная от профильного уровня грань, которая фактически является его обратной стороной.
Можно разделить такие швы по размерным нормам:
- катет;
- толщина;
- расчетная высота.
В угловом сварном шве для угловой сварки длина от уровня первой свариваемой детали до края шва на следующей детали и есть катет угольного шва. Катет относится к важным характеристикам, которые необходимо соблюдать в ходе сварных работ. При простых угольных соединениях с единым размером катет шва задается размером его краев. В сваривании тавровых конструкций катет имеет фиксированную величину, при этом используют единую размерность материалов. А при применении в сварных работах тавровых конструкций разной размерности он приравнивается к толщине более тонкого металла. Катет должен иметь правильные размеры для достижения максимальной крепости соединения, если пользоваться слишком большим катетом, то возможны сварные дефекты.
Начинающим можно упростить работу с деталями, расположив их для сварки «в лодочку». При сварке “в лодочку” сокращается вероятность появления подрезов, и замок получится прочнее.
Толщина угольного шва – это предельное удаление от его уровня до контакта предельного проплавления основного металла.
Что нужно помнить при сварке угловых соединений? Для угловых швов благоприятной считается вогнутая форма уровня с плавным переходом к основе. Это связано с проблематичностью проварки в угольных швах корня на всю толщину. В большинстве вариантов катет и толщину замеряют определенными лекалами.
Чтобы получить максимально прочное соединение, нужно ссылаться на множество факторов. Их учитывают при определении типа соединения в зависимости от необходимых характеристик свариваемых изделий.
Их применяют как при малоэтажном строительстве, так и при постройках больших домов, офисных и спортивных центров. При помощи сварки соединяют 2 или более деталей в 1. При этом образуется прочный и надежный шов, который может прослужить длительное время, не нарушаясь и не вызывая повреждения детали в целом.
Кроме того, сварные соединения и швы могут быть использованы, как для стыка металлических деталей из однородного типа стали, так и элементов, выполненных из различных сплавов. При таких сложных работах необходимо правильно подобрать технологию сварки, силу тока, расходные материалы (электроды). Кроме того, сварщик должен обладать достаточным опытом и умениями, чтобы не допустить прожига детали, избежать лишних напряжений и деформации в дальнейшей эксплуатации.
Классификация сварочных швов
Все сварные соединения нормируются специальной документацией, которая определяет понятия, области и места выполнения сварки. Описанная терминология применима для технической документации, которая прилагается по окончании выполнения швов. Эти же понятия указаны в учебных и методических пособиях, по которым производится подготовка сварщиков, а также дальнейшее обучение и повышение их квалификации.
Таблица классификаций сварных швов.
Используя общепринятые сокращения, даже при отсутствии документации по маркировке соединения или общей спецификации можно определить, какое именно сварное соединение выполнено в том или ином месте строительной конструкции. Приняты следующие условные обозначения: стыковые сварные соединения принято обозначать буквой «С», при выполнении шва внахлест – указывают «Н», если предусмотрены тавровые стыки, то на спецификации обозначено «Т», угловые – «У».
В основном сварочные соединения и швы принять разделять по нескольким признакам:
По виду конечной формы поперечного сечения:
- Стыковые, то есть свариваемые детали располагают по одной плоскости.
- Угловые, когда металлические детали находятся друг к другу под углом, при этом его величина значения не имеет.
- Прорезные, если детали, наложенные друг на друга, взаимно проплавляются. При этом одна из деталей (верхняя) проплавлена целиком, а другая часть сварного соединения (нижняя) лишь частично. Сам шов представляет собой заклепку. Это соединение еще называют электрозаклепочным.
По конфигурации при сварке:
- прямолинейного характера;
- криволинейного вида;
- кольцевого вида.
По длительности сварного соединения:
- Соединения, выполненные сплошным швом. Их длина колеблется от 300 мм до 1 м и более.
- Которые выполнены прерывисто. При этом расположение шва может быть по цепочке, в шахматном порядке, в зависимости от конструктивных особенностей детали и предъявляемых требований.
По способу применяемой технологии сварки:
- дуговая сварка без применения дополнительных средств (газа, флюса);
- сварка, выполненная в среде с наличием газа (например, аргона).
По количеству нанесения сварочных элементов:
- односторонний;
- двухстороннее соединение;
- многослойные.
По количеству металла, который образовался в результате наплавления:
- нормальное;
- усиленное;
- ослабленное.
Обычно нет строгого разделения по всем типам классификаций. При работе сварные соединения могут быть прямолинейные стыковые усиленные. То есть сочетания могут быть самыми разнообразными, в зависимости от сложности металлической конструкции, требований жесткости и надежности, наличия расходных материалов, а также мастерства сварщика.
Характеристика сварных соединений
Основные типы сварных соединений.
В зависимости от того, каким должен получиться в итоге, необходимо учитывать особенности его выполнения и технологию исполнения.
Стыковые сварные соединения представляют собой соединение деталей путем сплавления между собой. Детали располагают в одной плоскости и чаще всего применяют дуговую сварку. При этом такие швы могут быть использованы для соединения деталей с различной кромкой. Обработка кромки для сваривания зависит от толщины листа. Если в процессе выполнения работ требуется соединить детали различной толщины, то более толстый край должен быть скошен под размер меньшего. Это обеспечивает надежный шов.
По типу краев, которые участвуют при сваривании, стыковые сварные соединения можно разделить на:
- детали, которые не имеют скоса кромки. Они должны быть толщиной 3-5 мм;
- элементы, которые имеют криволинейную кромку;
- детали с кромкой, образующей букву «U», их толщина составляет 20-60 мм;
- детали, у которых кромка имеет вид «Х», толщина металла 12-40 мм.
Более подробно о соединениях
Стыковые сварные швы обладают самым низким значением напряжения, менее склонны к деформациям. Это обуславливает частое их применение. При выполнении стыкового соединения расход металла является минимальным, сама подготовка к работе должна выполняться тщательно и скрупулезно.
Тавровые элементы представляют собой соединения деталей из металла, когда одна из них расположена перпендикулярно к другой. Получается стык в виде буквы «Т». При таком типе сам шов может располагаться как с одной из сторон, так и с двух. Все зависит от требований жесткости, технической и конструктивной возможности произвести работы. Тавровые системы используются для сборки каркасов для ферм, различных видов колонн, стоек. Кроме того, такое соединение хорошо применять для сварки балок.
Угловые соединения выполняют в тех случаях, где элементы в конструкции не будут нести значительных напряжений. Например, при сварке емкостей, резервуаров. Чтобы обеспечить необходимую надежность и прочность, толщина свариваемого металла не должна превышать 1-3 мм. При угловом соединении детали прикладывают друг к другу под необходимым углом и сваривают. Величина угла не имеет значения. Шов проделывают двухсторонним сплошным таким образом, чтобы в него не могла проникнуть влага.
Нахлесточные соединения образуются тогда, когда детали расположены параллельно друг к другу. Шов при этом находится на боковых поверхностях металлических элементов. Кромки металла не нуждаются в дополнительной обработке, в отличие от стыкового метода. Расходы металла как основного, так и наплавляемого будут значительными.
Толщина самой конструкции при такой обработке составляет не более 12 мм. Для исключения проникновения влаги в само соединение его необходимо выполнять двухсторонним.
Швы при тавровом, нахлесточном, угловом соединении могут исполняться в виде маленьких отрезков, то есть точечным методом. Если надо сделать предварительные наплавления, то они выполняются круглой формы. Т.е. образуются при полном проплавлении одной из детали и частично другой.
Дополнительные моменты
Известные способы выполнения дуговой сварки без дополнительной обработки кромок могут быть произведены при толщине металла 4 мм при ручном виде работ, 18 мм – при механизированной работе. Поэтому если требуется сварить детали значительной толщины, используя ручную дуговую методику, то кромки необходимо дополнительно обрабатывать.
К элементам геометрии соединения можно отнести зазор, который присутствует между элементами, угол разделки, скоса и отклонение деталей, участвующих в сварке по отношению друг к другу. Угол скоса определяет угол разделки, который является определяющим для обеспечения необходимого доступа дуги на всю глубину шва, значит, полноценного выполнения самого шва. Величина угла в зависимости от типа соединения и метода обработки в основном колеблется в пределах 20-60 ° с допуском в 5 °. Величина зазора составляет 0-4 мм.
Если металл достаточно толстый, а зазор отсутствует, то может образоваться непровар.
А кромки, которые лишены притупления, могут привести к возникновению прожогов. При большом смещении деталей, процесс их сваривания может стать невозможным.
Окончательный выбор метода и способа, которым будут выполняться швы и соединения в металлической конструкции определяются ее сложностью и материалом исполнения. При проектировании, разработке смет на строительство, необходимо учесть эти особенности и при необходимости заложить использование дополнительных средств, которые обеспечат должную надежность и жесткость.
Сварным соединением называют совокупность деталей, соединенных сварным швом. При дуговой сварке применяют следующие виды соединений: стыковые, внахлестку, тавровые и угловые; в ряде случаев используются соединения прорезные, торцовые, с накладками, электрозаклепками (рис. 56).
Стыковые соединения. Стыковые соединения (рис. 56, а) являются самыми распространенными, так как дают наименьшие собственные напряжения и деформации при сварке, а также высокую прочность при статических и динамических нагрузках. Они применяются в конструкциях из листового металла и при стыковке уголков, швеллеров, двутавров и труб. Соединения встык требуют наименьшего расхода основного и наплавленного металла. При стыковых соединениях нужна тщательная подготовка листов под сварку и достаточно точная подгонка их друг к другу.
Листы толщиной 1—3 мм можно сваривать встык с отбортовкой, без зазора и без присадочного металла (рис. 56, б).
При ручной дуговой сварке стальных листов толщиной 3—8 мм кромки обрезают под прямым углом к поверхности, а листы располагают с зазором 0,5—2 мм.
Без скоса кромок можно сваривать встык листы до 6 мм при односторонней и до 8 мм при двусторонней сварке.
Листы толщиной от 3 до 26 мм при ручной дуговой сварке сваривают встык с односторонним скосом одной или двух кромок. Этот вид подготовки кромок называется V-образным. Листы толщиной 12—40 мм сваривают с двусторонним скосом кромок, называемым Х-образным при скосе обеих кромок и К-образным при скосе одной кромки.
Кромки притупляют с целью предотвратить протекание металла при сварке (прожог). Зазор между кромками оставляется для облегчения провара корня шва (нижних частей кромок). Большое значение для качества сварки имеет сохранение одинаковой ширины зазора по всей длине шва, т. е. соблюдение параллельности кромок.
Двусторонний скос (Х-образный) имеет преимущества перед односторонним (V-образным), так как при одной и той же толщине
Листов объем наплавленного металла будет почти в два раза меньше, чем при одностороннем скосе кромок. Соответственно уменьшится расход электродов и электроэнергии при сварке. Кроме того, при двустороннем скосе кромок возникают меньшие коробления и остаточные напряжения, чем при одностороннем. По
Листов объем наплавленного металла будет почти в два раза меньше, чем при одностороннем скосе кромок. Соответственно уменьшится расход электродов и электроэнергии при сварке. Кроме того, при двустороннем скосе кромок возникают меньшие коробления и остаточные напряжения, чем при одностороннем. Поэтому листы толщиной свыше 12 мм лучше сваривать с Х-образным скосом кромок. Однако это не всегда осуществимо из-за конструкции и размеров изделия.
При ручной дуговой сварке стали толщиной 20—60 мм применяют также криволинейный U-образный скос одной или двух кромок с целью уменьшения объема наплавленного металла, что увеличивает производительность сварки и дает экономию электродов. При сварке встык листов неодинаковой толщины более толстый лист скашивается в большей степени (рис. 56, в).
Соединения внахлестку. Соединения внахлестку (рис. 56, г) преимущественно применяются при дуговой сварке строительных конструкций из стали толщиной не более 10—12 мм. В отдельных случаях их используют и при сварке листов большей толщины (но не свыше 20—25 мм). Соединения внахлестку не требуют специальной обработки кромок, кроме обрезки. В таких соединениях рекомендуется по возможности сваривать листы с обеих сторон, так как при односторонней сварке в щель между листами может попасть влага и вызвать последующее ржавление металла в сварном соединении.
Сборка изделия и подготовка листов при сварке внахлестку упрощаются, однако расход основного и наплавленного металла больше, чем при сварке встык. Соединения внахлестку менее прочны при переменных и ударных нагрузках, чем стыковые. При роликовой и точечной контактной электросварке в основном применяют соединения внахлестку.
Угловые соединения. Такие соединения (рис. 56, д) применяют при сварке по кромкам, расположенным под прямым или иным углом друг к другу. Используются, например, при сварке резервуаров, емкостей, сосудов, фланцев трубопроводов и других изделий, работающих под небольшим давлением (ниже 0,7 кгс/см 2), неответственного назначения. Иногда угловые соединения проваривают также и с внутренней стороны. Для металла толщиной 1— 3 мм можно применять угловые соединения с отбортовкой и сваркой без присадочного металла.
Тавровые соединения. Тавровые соединения (рис. 56, е) широко используются при дуговой сварке балок, колонн, стоек, каркасов ферм и других строительных конструкций. Выполняются без скоса и со скосом кромок одной или двух сторон. Вертикальный лист должен иметь достаточно ровно обрезанную кромку. При одностороннем и двустороннем скосе кромки между вертикальным и горизонтальным листами оставляется зазор для лучшего провара вертикального листа на всю толщину. Односторонний скос нужен в том случае, если конструкция изделия не позволяет произвести сварку таврового соединения с обеих сторон. В соединениях без скоса кромок возможен непровар в корне шва, поэтому такой шов может разрушиться при вибрационных и ударных нагрузках. В тавровых соединениях со скосом кромок обеспечивается необходимая прочность при любых видах нагрузок.
Прорезные соединения. Эти соединения (рис. 56, ж) применяются, когда длина нормального шва внахлестку не обеспечивает достаточной прочности. Прорезные соединения бывают закрытого или открытого типа. Прорезь может выполняться кислородной, воздушно-дуговой и плазменной резкой.
Торцовые, или боковые, соединения. Такие соединения показаны на рис. 53, з. Листы сваривают по смежным торцам.
Соединения с накладками (рис. 56, и). Накладка 2, перекрывая стык листов 1 и 3, приваривается по боковым кромкам к поверхности листов. Эти соединения требуют дополнительного расхода металла на накладки и поэтому применяются только в тех случаях, когда не могут быть заменены стыковыми или нахлесточными соединениями.
Соединения электрозаклепками. При помощи электрозаклепок получают прочные, но не плотные соединения (рис. 56, к). Верхний лист пробивается или просверливается, и отверстие заваривается так, чтобы был захвачен нижний лист. При толщине верхнего листа до 3 мм его предварительно не просверливают, проплавляя дугой при сварке заклепки. Электрозаклепочные швы применяют в нахлесточных и тавровых соединениях.
Описанные соединения являются типовыми для рунной дуговой сварки стали. При газовой сварке, сварке под флюсом, сварке легкоплавких цветных металлов и в других случаях формы кромок могут быть иными. Сведения о них приведены в последующих главах при описании этих способов сварки.
Формы подготовки и углы скоса кромок, зазоры и допускаемые при этом отклонения для швов сварных соединений при ручной дуговой сварке регламентируются ГОСТ 5264—69.
Виды швов. Существуют следующие виды сварных швов:
1. По положению в пространстве — нижние, горизонтальные, вертикальные и потолочные (рис. 57, а). Наиболее простым по выполнению является нижний шов, наиболее трудоемким — потолочный. Потолочные швы могут выполнять сварщики, специально освоившие этот вид сварки. Выполнять потолочные швы дуговой сваркой труднее, чем газовой. Сварка горизонтальных и вертикальных швов на вертикальной поверхности несколько сложнее, чем сварка нижних швов.
2. По отношению к действующим усилиям — фланковые, лобовые, комбинированные и косые (рис. 57, б).
3. По протяженности — непрерывные и прерывистые (рис. 57, в). Прерывистые швы применяют в тех случаях, когда соединения не должно быть плотным, а по расчету на прочность не требуется сплошного шва.
Длина отдельных участков прерывистого шва (l) составляет от 50 до 150 мм; расстояние между участками шва обычно в 1,5— 2,5 раза больше длины участка; величина t называется шагом шва. Прерывистые швы применяют довольно широко, так как они обеспечивают экономию наплавленного металла, времени и стоимости сварки.
4. По количеству наплавленного металла или степени выпуклости— нормальные, выпуклые и вогнутые (рис. 57, г). Выпуклость шва зависит от типа применяемых электродов: при сварке тонкопокрытыми электродами получают швы с большой выпуклостью. При сварке толстопокрытыми электродами, вследствие большей жидкотекучести расплавленного металла, обычно получаются нормальные швы.
Швы с большой выпуклостью не обеспечивают прочность сварного соединения, особенно если оно подвергается переменным на жидкотекучести расплавленного металла, обычно получаются нормальные швы.
Швы с большой выпуклостью не обеспечивают прочность сварного соединения, особенно если оно подвергается переменным нагрузкам и вибрациям. Это объясняется тем, что в швах с большой выпуклостью нельзя получить плавного перехода от валика к основному металлу и в этом месте образуется нечто вроде «подреза» кромки, где и происходит концентрация напряжений. При действии переменных ударных или вибрационных нагрузок с этого места может начаться разрушение сварного соединения. Швы с большой выпуклостью неэкономичны, так как на их выполнение расходуется больше электродов, времени и электроэнергии.
5. По типу соединения - стыковые и угловые. Угловые швы применяются при выполнении соединений внахлестку, тавровых, угловых, с накладками, прорезных, торцовых. Сторона к углового шва (рис. 58) называется катетом.
При определении катета к в швах, изображенных на рис. 58, а, принимается меньший катет вписанного в сечение шва треугольника; в швах, показанных на рис. 58, б и в, принимается катет вписанного равнобедренного треугольника.
ГОСТ 5264-80 допускает выпуклость шва е: при нижнем положении сварки - до 2 мм, при ином положении сварки — до 3 мм. Приращение катета (m - к) при любом положении шва допускается до 3 мм.
Администрация Общая оценка статьи: Опубликовано: 2011.06.01